LiNC80 SBC1 kits are available for purchase!
I am proud to announce that as of now, my LiNC80 SBC1 is available for purchase in kit form at Tindie!
It took me a few tries to get through the approval process, simply because the fairly high differences in the fairly high shipping costs incurred from using Posten Norge as my trusted carrier, forced me to make separate listings of Kit and PCB, and that caused issues, as Tindie weren't used to dealing with that.
I'm not sure if this is the culmination of or the start of a lot of hard work. Now starts the bit where I need to ship, restock, support and see what people make of it. But first of course the terrifying bit: will anyone actually purchase the kit?
If you want a compact, expandable, fun 8-bit retro computer reminiscent of 1979, head on over to my Tindie shop now!
Digital I/O card for my Z50Bus computer
While working towards getting my LiNC80 SBC1 kits ready for sale, I had a little bit of waiting-time to cover. During that time, Steve Cousins and I were talking about his boot-up status output using a standard I/O port, and that it would be nice if I would be able to provide a digital I/O card a short time after launching the kits.
As I already had my prototype prototyping cards and a bit of time, I designed a card inspired by Spencer's RC2014 Digital I/O card, and assembled it using simple point-to-point wiring. As expected, the card performs exactly what it was designed to do, both when connected directly to the SBC and when connected to a 5-slot Z50Bus backplane.
This is a simple I/O card that uses a 74LS273 latch to receive and store output data displayed on eight LEDs, a 74LS245 bus tranceiver to "gate" the input switches/buttons as inputs, and a 74LS688 8-bit comparator to do full address decoding of 8 bits. The way the 8-bit comparator is used makes it possible for this card to use any single I/O address in the Z80 I/O address range. Writing to the selected address sets the output state, and reading the address reads the current values on the buttons/switches. Steve's SCMon uses the "reserved" address 0x30 as a simple output write port for status during boot, so setting this card's address to 0x30 allows the nice led-scroll to be seen 🙂
Based on the schematic below, I will start doing a PCB layout, and make this an official LiNC product as soon as the LiNC80 SBC1 launches proper.
Adapters and addons to my 8-bit micro
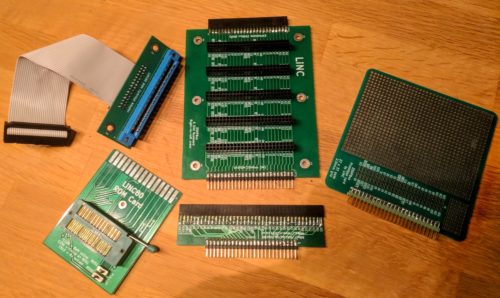
A collection of addon- and adapter cards
While testing my homebrew computer, I made some home-made addons, both in form of perf-board construction and home-etched PCB. I actually also made a connector-on-cable adapter, where I soldered the individual lines of a 30-pin ribbon cable onto an 805-series card-edge connector on one end, and because I failed to properly crimp an IDC connector on the other, I ended up soldering all 30 pins on that side as well. The other home-made adapters I made were: parallel input tester (perf), parallel output tester (perf), adapter from Z50Bus to RC2014 backplane (perf) and ROM Cartridge (PCB).
Considering how good the PCBs I got manufactured for the LiNC80 SBC1 itself, and how much effort went into making the Z50Bus-RC2014 adapter, I decided I wanted to get manufactured a set of support cards for the machine, and make it all look just as good. Additionally, having these support cards available would mean that I could have a small «ecosystem» of parts for future kit availability.
ROM Cartridge
The first card I designed was the ROM Cartridge PCB. The design I sent to manufacture for that was simply a slight tweak of the design I had already etched for testing, so it made sense to complete that first.
![]() DIY etched ROM Cart |
![]() Manufactured ROM Cart PCB |
The card is designed to be large enough to comfortably insert and remove. It has a 28pin location for either a direct soldered or socketed ROM chip, and a central mounting hole for encased cartridges. The two two-position jumper locations allow for any ROM chip size between 16 and 64kByte, taking advantage of the LiNC80 ROM Bank select signals for ROM sizes above 16kByte. If the intended ROM application fits in a 4k or 8k chip, it’s naturally no problem to use chips of those sizes, as the pinout on the connector is JEDEC compliant.
Two jumpers are also on the board, making the choice of ROM chip size flexibility possible, and at the same time giving access to (and control over) the ROM bank select signals on my rom slot connector.
ROM Cartridge Slot
As I mentioned, I hand-soldered ribbon cable onto connectors to test the ROM Slot functionality of my design. Anyone who has tried soldering ribbon cable knows how much pain that is. To anyone who has not tried: avoid it if you can. So to spare anyone else from the unpleasant soldering task, I made up a simple passive IDC-to-Cardedge adapter.
I decided to go with male header pins on the PCB, and use a ribbon cable with female IDC connector on both ends. Mounting IDC connectors can be easily done with a simple vise as a replacement for expensive pressing tools. A simple guide on how to do the vise approach can be found at https://startingelectronics.org/articles/IDC-ribbon-cable/
This is a purely passive adapter, with a pin-for-pin connection for all 30 pins. This means it can also be used as a general pinheader/IDC-to-cardedge adapter in addition to its intended use.
5 Slot Z50Bus
When I first started my design, and came up with the Z50Bus, I realized that I would have to make some kind of bus back-plane card. For this first iteration/version, I decided to make a purely passive one, without any bus buffering built in. I didn't even provide locations for decoupling capacitors, leaving the responsibility for those kinds of things to the expansion cards.
The back-plane has 5 standard slots. Connection to my computer on the right-hand side because the expansion connector on that board is on the left... On the left hand side of the back-plane is an extension header, meaning in theory, multiple cards can be added in a chain.
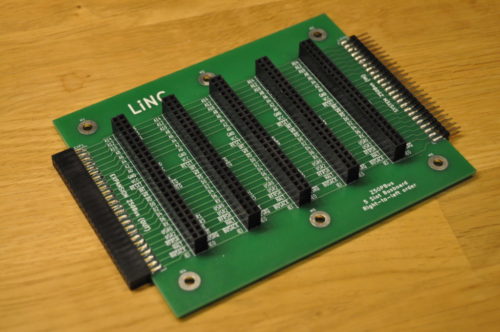
5-slot backplane
Speaking of chains. The Interrupt Chain signals IEI/IEO on this card are connected in a right-to-left order. This makes the first slot be on the right-hand side of the card, closest to the Z50Bus host.
Prototyping card
With a back-plane available, it would be nice to have some compatible expansions. Unfortunately, I hadn't made any of those yet. And I had quite early on realized that my choice of dual-row headers for the bus made prototyping more difficult than if i had gone for single-row. The natural step from this, was to make a made-to-fit prototyping perf-board!
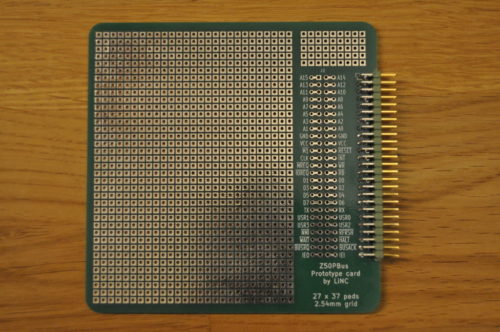
Prototyping card
My board provides a main prototyping area of 27 by 37 individual pads on a standard 2.54mm grid, plus an additional grid of 9 by 5 pads. The 50-pin bus connector is broken out on easily accessible connection points, providing two connecting pads per signal. I chose to make the board exactly 100x100mm. The real reason for this size is that most DIY-friendly board manufacturers have especially low prices for boards up to (including) just that size.
Adapter for RC2014
Because I already had built an RC2014 kit, as well as a couple of addons for that system, I felt it made sense to be able to test my expansion bus using those. i had after all designed the bus to be relatively compatible. During building and testing, I created a perf-board version of an adapter, with pin-to-pin wiring. This worked, but it was fragile. In the picture below, you can see this prototype connecting my Revision A computer to an 8-slot RC2014 backplane (not shown is that it works, and runs RC2014 ROM software off the backplane).
Because this is a trivial adapter, it was a simple design. I tried to compress it without making it DIY-unfriendly. As part of the design, I added pads allowing selection of horizontal or vertical mounting of the RC2014-side of things. On the Z50Bus side of things, I decided to use on-edge mounting of the header simply because I like that style.
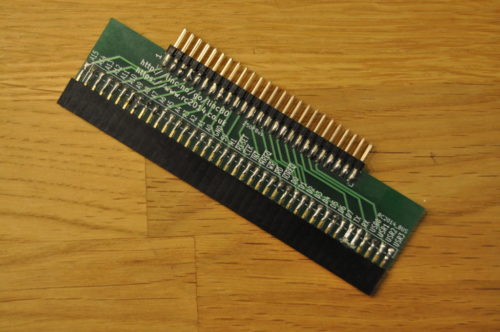
Bus-adapter card
I made a mistake in the design of this one. It's not a problem for most add-on cards, but it caused me problems when I tried to test the adapter. My mistake was to wire ALL signals for the simple RC2014 bus straight to the Z50Bus. Including the RX and TX lines. When I tried testing the MC68B50 serial card on the adapter, my system would seemingly not boot. I struggled for a while trying to figure that out, until I realized... The MC68B50 UART and the SIO/2 DUART were both connected to those lines. And both were trying to drive the lines! So my system was booting, but my terminal could not see that, and could not talk to the UART either. By cutting the two traces for RX and TX respectively, I had no problems with any of the modules I had to test. Even running a «Full monty» RC2014 on the RC2014 backplane, using the LiNC80 as just CPU and RAM worked without any issues.
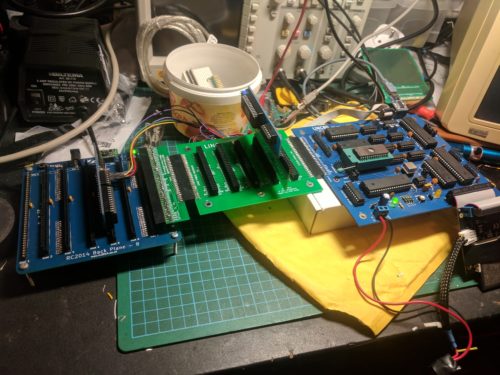
Creative combinations of back-planes, adapters and modules
I may do an update of this board, with jumpers or solder-pads on those two lines, but as long as the user is aware that adding multiple UART chips on the same lines cause problems, I think the current version will work fine.
Before I add my closing line... I am really gearing toward making kits! They aren't quite available for sale yet, but the product presentations and documentation is coming up on my business-site! To start navigation directly from the LiNC80-pages, go to http://linc.no/go/linc80. To see what else I have on offer, see http://linc.no/products, where you also can find the more "official home" of the Z50Bus specification and accessories
This post is part of a series documenting my journey in making my own homebrew computer, the posts can be found on this link.
The birth of my Z80 computer design, the LiNC80 SBC1
I originally started my adventure of homebrew computer building thinking I'd build a relatively simple system. This thought soon changed, as I outlined in the "scribbling ideas" post. The main reason for daring to be more ambitious was basically that with a good base design like the "Fully functional Z80 CP/M machine using only 9 chips" from Grant Searle, and a bit of experience, it seemed to be well within reach! Grabbing the list from the "scribbling ideas" post, my top-level selection of features ended up with this:
- Z80 CPU
- Zilog SIO/2 serial port controller with dual serial ports
- Zilog CTC for four channels of Counter/Timer, 2 of them dedicated to the SIO/2
- Zilog PIO for two Parallel ports
- Expandable system through Z50Bus
- Memory map designed to allow for graphics expansion
- CP/M compatibility
- ROM part of memory from address $0000 disable-able (needed for CP/M and more)
- For fun, a dedicated ROM Cartridge connector
- Z80 Interrupt Mode 2 in the core
- Compatibility with software from Grant Searle (for easy system bring-up)
In addition to that list, I set a limitation of component selection, all active components had to be currently active parts available as new from manufacturer. I also wanted to use static RAM, and have 64KByte of it in DIP packages, so the design uses two 32kx8 SRAM ICs.
I'm really not much of a software-guy. I can program, and I know my way around assembler code, but I am most definitely not one of those guys that can code a ROM Monitor in an evening. Being able to re-use existing software helps me get my system up and running. The fact that Grants software works well, on a system that can run an operating system I want to use, means it would be silly of me to not take advantage of that. Because that existing software uses IM2, I would have to use IM2 as well, or commit to some serious software redesign. Besides, I wanted to try out IM2 more because I think it's cool. My desire to run CP/M also dictates the need to have a way to disable (or move) ROM out from address $0000 of the memory-map.
The "dependency effect" of using existing code also makes itself visible in hardware I/O address selection. To avoid changing too much code, it makes sense for me to place the SIO/2, ROM-disable and CF-disk I/O addresses on the same addresses used in Grant's design. I also liked his approach of using a 74LS138 for decoding, so I stuck with that approach, and selected "remaining" decode outputs for use with the CTC and PIO. The decoding logic ends up "eating up" 8 I/O addresses for each "on-board device", so 40 I/O addresses in the ranges 0x00 to 0x1F and 0x38 to 0x3F are locked. Somewhat expensive in terms of resources, but it allows for a simple construction with few parts. Besides, all addresses from 0x40 and up to 0xFF are still available for expansions.
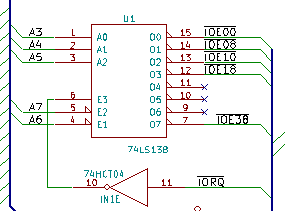
I/O address decoding for on-board devices
As listed, I wanted to be able to use software-controllable bit/baud rates on the serial ports. To be able to do that I chose to include the Z80CTC, a counter/timer controller, to drive the SIO. But I wasn't quite sure about my Z80 assembly skills yet, so I decided to include a jumper-selector to select SIO-clock to be CPU clock or CTC. That way, I could select CPU-clock for booting unmodified code from Grant, and then switch to CTC-clock once I knew how to do that.
My first major divergence from the base design came as a result of my desire to have a memory map designed for graphics. Being able to combine that with the option of running code other people has made for Grant's design, meant that I had to include some kind of bank-switching. The design already included a very basic form of bank-switching: Grant has designed the "disable ROM" feature as a simple RS-latch that bank-switches the lower 16k between ROM and RAM. To switch from the ROM bank to the RAM bank, a write to address 0x38 needs to be done. In his design, the bank switch is triggered by an I/O write to the correct address, and the data is not used for anything. I examined the source code and found out that even if you only need to write something to the address, his code actually writes the value 0x01. Based on that, I decided that my "memory management" for bank-switching could be done using some kind of register, placed at 0x38, as long as the lowest bit of the register was used for enabling/disabling ROM. This would additionally give me the option of switching ROM back in, in contrast to Grants design where only a system reset would bring ROM back into active memory.
Armed with a general idea on how I could do bank-switching, I started looking at how I could make a memory map that worked with both CP/M and graphics. Because CP/M needs to have its BIOS and BDOS placed in a predictable, always available location in memory, and it expects RAM in the bottom of memory, my options were a bit limited. On top of that, I wanted to at least start with existing software, and the software I had available expected to be able to stuff BDOS, BIOS, ISRs and stack in the top 8-16k of memory. That made me decide to use a fairly odd and uncommon memory map. I decided that the second-top-most 16k would be the "window" for bank-switching. Basically, bottom 16k is switchable RAM/ROM, second 16k is always on-board RAM, third 16k is switchable memory defaulting to on-board RAM, and fourth and final 16k is always on-board RAM.
With the general memory map laid out, I turned my attention back to that register I talked about earlier. I decided I'd go for the simplest approach I could think of, one that I had used to implement a simple digital-out solution for the RC2014 computer. By using a 74LS273, I could get a very simple 8-bit write-only register. To quote the data sheet: «The SN54/74LS273 is a high-speed 8-Bit Register. The register consists of eight D-Type Flip-Flops with a Common Clock and an asynchronous active LOW Master Reset.». Placing one of those on I/O address 0x38, using IO Write as clock input and the data bus as D-inputs, I could use the outputs to perform bank switch selection. Using the system RESET signal for the '273s Master Reset, the system would always reset to a predictable state. And by using the lowest bit to control ROM disabling, I had compatibility with the existing code from Grant! With seven bits still available, I decided to use three bits for RAM bank select. This would let me simply use another LS138 to select one of eight RAM banks, and by using "location 000" for the on-board RAM, things should boot nicely.
I selected to use one bit of the "register" to control Interrupt Enable Input of onboard devices. This would let me "lock" interrupts to an IM2 disabled state, a feature I thought would be handy to have on top of the Interrupt Enable / Disable Interrupt instructions of the CPU. This left me with a few bits left over. In my scribbling, the idea of having a ROM cartridge for fun and experimentation had been added. I quickly added to that idea, by using two of the bits as "off-board ROM bank selects". That would allow a ROM cartridge to have four 16k banks! Which by the way matches nicely with a standard 64Kbyte ROM chip size.
With memory map idea fleshed out, I had to figure out a way to make the memory decode and interfacing work. I ended up finding a cool tool at https://simulator.io/ that allows for on-line simulation of digital logic. Using first a set of logic tables, I assembled an idea, and implemented it on simulator.io first, before adding it to my design. You can see and play with the result at https://simulator.io/board/RoLQ8QDEei/2. Confident that I had a memory layout that could work, and a decode logic that seemed to make sense, I started the actual design. The resulting memory interfacing logic took quite a bit more glue logic than Grants simple design, but I think it came out quite nice.
The overall schematic I had in KiCAD was at this point starting to get large and complex. Thinking back at my issues with flaky breadboards, I was starting to dread building something as complex as this on either wonky breadboards, or on a very large perf-board. It would be doable, but the thought of debugging soldered point-to-point or bad breadboard connectors didn't really sound tempting. At the same time, I was still learning to use KiCAD for a somewhat large design, and I more or less accidentally started laying out a PCB. Combining manual parts layout, a bit of manual routing and experimentation with freerouting, I suddenly had a board layout that looked decent. So I took a gamble, and simply sent off some money and a few gerber files to seeed studio. Not a full week later, I received a box containing five fine looking PCBs.
This board was designed with all the bullet points from the design list. There's SIO/2, CTC and PIO devices, an IDE connector, and on the right side, a Z50Bus expansion bus. Additionally, I created a different version of an expansion connector on the left side that included all the decoded bank-switching lines (but not all CPU-signals, to keep it on a 50-pin connector).
Seeing how nice my PCB looked, I got to work assembling it. I soldered in passives, added sockets for IC's, and completed all soldering. After some experience with how much rosin flux can affect a complex logic circuit, I cleaned the board thoroughly before adding any of the semiconductor components. Finally, I hooked up serial ports and applied power.
Nothing happened.
Or, well, something happened. The board started drawing current, and it was well within expected range. So it would seem that the reason for it not working wasn't a dead short or a major defect. It had to be some kind of logic design flaw. I got a hold of a cheap logic analyzer to try to figure out what was wrong, but I couldn't get the analyzer to trig properly on the T1-T3 multi-clock-per-instruction that the Z80 has. I shelved the project in frustration for a while. After some months of not working on it, I brought it back out, and started poking around. After seeing some weird behavior, and a bit of "almost working" if I removed both the 'LS138 and the 'LS273, I figured something was weird with the I/O addressing. On examining the schematic in detail, I realized I had made two really silly mistakes.
The I/O address decoder was always active, doing its decoding even on Memory operations and even on the built-in DRAM refresh. Next, the 'LS273 that I was using as my "configuration register" only used the I/O address decode signal as its "Write" signal! These two problems together meant that the contents of the "register" was constantly changing. I'm not surprised that the code in ROM was less than happy about getting bank-switched out half-way through an instruction... Fortunately, I had spare logic elements in the glue logic IC's. This allowed me to fix the problems using bodge-wires and cut traces on the back of the PCB. The same evening I discovered my errors the system started doing what I had intended, and I had working CP/M on my slick-looking homebrew PCB.
I decided it would be best to fix the mistakes in my schematic, so I went back to KiCAD and implemented the changes that I had made on the board. I swapped some gate selection around to make the glue logic easier to route. While I was looking at the routing issues, I had a long think about the whole "two expansion ports, one for system and one for graphics". In the end, I decided it did not really make sense. I could put all the memory/bankswitch and graphics-only signals on a much smaller header connector, and use a cable to a standard Z50Bus expansion card. That would mean only one expansion connector would be needed. This in turn would lead to much simpler routing of the board, and the board could be physically smaller, reducing cost.
Reducing cost may sound weird. After all, this is my homebrew design, and I already had a working computer in front of me. But at this point, I was seriously considering making this a kit. And if I was to sell any of these, making the cost of the PCB go down would be a good plan. So, the changes were implemented, I did a new layout, and sent it off to seeed for fabrication. 10 days later I got a new batch of boards that I fairly quickly assembled. I transplanted all ICs from the previous build over, and tested it.
And it did not work. ARGH!
Back to the schematic, I found ONE silly mistake. While I was redesigning, I had done some changes to the schematic around the SIO/2 chip, and while doing that, I had swapped the address lines A0 and A1 by accident. That meant that the Control and Data addresses had become swapped. A quick cut-and-solder on the PCB swapped those back, and the computer came to life! I set to work writing code to test the other on-board devices that aren't on Grants design. I got the CTC to clock and generate interrupts, and I got the PIO to work as Byte-out, Byte-in, and bit-in-out. But no matter what I did, I could not get the PIO to generate interrupts.
It turns out, the PIO interrupt signal is gated by its M1 input. And, because the PIO actually has one pin less than it needs, Zilog chose to make a multiplexed M1+Reset function on the M1 pin. And in my design, I had thought "M1 input is active if either CPU M1 is active OR if system Reset is active". So I had put an OR gate there. There's one problem with this. Both Reset and M1 are ACTIVE LOW signals. And to make an "or" function for active low signals, you need to use an "and" gate! Long live boolean logic and active low signals. Who would have thought OR to be different from AND in boolean logic... I managed to finagle this by more bodging, and eventually I had a fully working computer, where all on-board devices worked.
Considering the amount of self-inflicted troubles I had experienced so far, I decided to test the expansion bus and the ROM cartridge connections before fixing my schematic again. To my relief, both of those worked without problems. I was able to use a ROM cartridge with ROM bank select, and was even able to use the RC2014 backplane to test using off-board memory and off-board devices.
During the testing of the ROM cartridge solution, I discovered that the rule of only using parts still in production had been violated on my design. I had based the on-board ROM circuit on a 16Kx8 EPROM, the 27c128. That ROM chip is not available, and neither is it's EEPROM-version, the 28c128. Fortunately for me, the bigger AT28C256 is still in production, and very close to pin compatible. I revised the schematic and board to include two jumpers for on-board ROM allowing either tied VCC signal for 'c128-devices, or use of the ROM-select lines. This makes it possible to select between 'c128, 'c256 and 'c512 ROM chips (16k, 32k and 64k), and even use of bank switching for on-board ROM. The physical placement of the jumpers was done so a ZIF-socket would fit (it's tight, but it fits), just because I could.
Considering the errors in this revision B of the board, I made corrections, and created revision C. This board now carries my official name for my homebrew computer design as it stands today: the LiNC80 Single Board Computer 1 Rev C. Considering it is an expandable board, with no on-board graphics, it may seem strange that I call it an SBC. Before the arrival of a heap of BeagleBoard and Raspberry Pi like devices, it was usual to call a PCB that implemented a fully working embeddable computer an SBC, and it was unusual for SBCs to have local graphics, but not unusual for them to have expansion/interface connectors.
Revision C of the board still has a minor issue, but none that makes a real difference to a system user that is aware of it. The only significant problem I see at the moment, is related to how the two serial ports behave on RTS/CTS signals if one of the ports is left unconnected. On the board, there is a jumper that selects between honoring incoming CTS (RTS from other host), or tying it to Gnd. If unconnected and not tied to Gnd, the SIOA tends to lock up the second serial port SIOB. On the other hand, if SIOA is connected, but SIOB is left unconnected, random characters may get generated if the CTS input is floating. The solution is to jumper the unused CTS signal to "disabled" for an unconnected SIO port.
This post is part of a series documenting my journey in making my own homebrew computer, the posts can be found on this link. Stay tuned for more posts in this series. The next will probably be about the various adapter cards I have planned/made.
Note! I am gearing toward making kits available!
The product description pages for the kit starts off at http://linc.no/products/linc80-sbc1/
The new, more official page for the Z50Bus is located at http://linc.no/products/z50bus
Z50Bus – A compact expansion bus for 8-bit microcomputers
Note!
The new, more official page for the Z50Bus is located at http://linc.no/products/z50bus
The Z50Bus is a suggestion for a system expansion bus for 8-bit microcomputers. First, a little background. It came into existence early in my design phase of my own homebrew computer. As such it is a new bus layout, and my personal needs is reflected in its layout. I wanted an expandable system, I wanted it to have a documented bus layout to allow others to design around it, the bus should be electrically simple, and require few logical components to implement. To satisfy the criteria of being simple and require few components, the layout needed to be close to the CPU I intended to use. As a result of that, the bus is closely tied to the CPU signals of the Zilog Z80 CPU. I investigated using an existing bus layout. The standardized bus layouts that I found to be relevant were S100[1][2] and STD80[1][2] or the 56-pin variant of the STD bus, as used by the Ferguson Big Board II shown at the bottom of this post. In my opinion, using any of these would require more complexity than I wanted. Following the actual standards would also be required, which would require the use of 100-, 80- or 56-pin edge connectors, and including voltage levels that seem weird in modern systems. Most of +8V, +16V and -16V, +12V and -12V would need to be included. I also looked to the popular homebrew kit system RC2014. Its bus layout is very simple, and with a SIL-like connector, it's very easy to make prototypes for the system. What I don't like about the bus, is that the standard version does not implement all useful CPU signals, and the physical rigidity of the connectors is weak. So, I wanted to use a pin-header based connection that is more rigid than a single row, and at the same time let the width of the physical connection be fairly small.
The name of the Z50Bus comes from being originally designed to use a 50-pin connector to integrate a system around a Z80 CPU. Being a simple bus specification, it is possible to use/integrate it with other 8-bit CPUs using some glue logic. One such example is shown later, for using a 65C02 CPU.
Signal levels and descriptions
Signal levels are 5V Single Ended, with HC TTL levels expected. So, each signal uses a single line, and an active high signal will have a High at 3.5V - 5V, and a Low state at 0-1V. The 5V and GND lines are the only supply voltages on the bus. System implementations should make sure these are noise-free, well decoupled, and dimensioned for the system current draw.
The bus uses a double-row connector scheme, with the following pin layout
Pin | Signal name | Pin | |
1 | A15 | A14 | 2 |
3 | A13 | A12 | 4 |
5 | A11 | A10 | 6 |
7 | A9 | A8 | 8 |
9 | A7 | A6 | 10 |
11 | A5 | A4 | 12 |
13 | A3 | A2 | 14 |
15 | A1 | A0 | 16 |
17 | Gnd | Gnd | 18 |
19 | 5V | 5V | 20 |
21 | /M1 | /Rst | 22 |
23 | Clock | /Int | 24 |
25 | /Mreq | /WR | 26 |
27 | /IOreq | /RD | 28 |
29 | D1 | D0 | 30 |
31 | D3 | D2 | 32 |
33 | D5 | D4 | 34 |
35 | D7 | D6 | 36 |
37 | Tx | Rx | 38 |
39 | Usr1 | Usr0 | 40 |
41 | Usr3 | Usr2 | 42 |
43 | /NMI | /Refresh | 44 |
45 | /Wait | /Halt | 46 |
47 | /BusRQ | /BusACK | 48 |
49 | IEO (*) | IEI (*) | 50 |
Female bus - Male card
* Note that IEO/IEI forms an Interrupt Enable Chain, where the IEO of a higher priority card needs to connect to a lower priority card. This means a bus board needs to connect IEO of one "slot" to the IEI of the next. It also means cards need to be present "in order", or empty slots need IEI/IEO jumpered for interrupts to work.
This layout of the signals is relatively simple to lay out for both CPU and expansion cards. Additionally, it is easily "unfolded" onto a single-row implementation, where using the first 42 pins mapped onto a 1x40 connector gives full compatibility with the bus layout of the RC2014 compatible ecosystem.
The on-bus signals function/description closely follow Z80 CPU signals, with a few extra signals inspired/compatible with the RC2014 signal set:
D7..D0 | Data bus lines |
Clock | System / CPU Clock (Phi2Out for 6502) |
/Rst | System Reset, Active Low |
/Mreq | Memory Request, Active Low, CPU Output |
/IOreq | IO Request, Active Low, CPU Output (synthetic for 6502) |
/WR | Write, Active Low, CPU Output |
/RD | Read, Active Low, CPU Output |
/M1 |
Machine Cycle One, Active Low, CPU Output (M1+IORQ active indicates INTAck. May use SYNC on 6502)
|
/Int |
Interrupt, Active Low, CPU Input, device requests interrupt by pulling INT low.
|
/NMI |
Non Maskable Interrupt, Active Low, CPU Input, device requests interrupt by pulling INT low.
|
/Wait |
Wait, Active Low, CPU Input, used to hold the CPU for wait states (can integrate RDY for 6502)
|
/Halt |
Halted, Active Low, CPU Output, indicates that the CPU is in WAIT FOR INTERRUPT state (HALT or WAI instructions)
|
/BusRQ |
Bus Request, Active Low, CPU Input, used to request bus control, i.e. for DMA
|
/BusACK |
Bus Acknowledge, Active Low, CPU Output, indicates that a BusRQ is accepted, and that CPU signals are high-Z
|
/Refresh |
DRAM Refresh cycle, Active Low, CPU Output. When Refresh and Mreq are active, a DRAM refresh can be done
|
IEO (*) |
Interrupt Enable Out, Active High output from one expansion card to next expansion.
|
IEI (*) |
Interrupt Enable In, Active High input to expansion from previous expansion card or system/CPU board
|
Tx / Rx | System internal TTL Serial |
Usr0..Usr3 |
User Definable pins (USER1...4 on RC2014, note numbering difference)
|
The signal layout for Z50Bus is simplistic, and makes very little attempt at being a signal balanced and noise cancelling bus design. The bus specification itself does not indicate if a system should use buffered bus or buffered expansions (or be raw CPU signals).
Mechanical implementation and suggestions
The standard bus connector to be used, is 50-pin dual-row header pin and socket, with 2.54mm pin pitch. For expansion cards that plug into a busboard, a Male pin header with nominal 6mm pin length should be used ("standard" header, sometimes called 11mm). The bus-side connector should be a Female PCB Header Socket, with nominal 8.5mm height.
The suggested arrangement for expansion cards is to use a Right angled connector. For orientation, an expansion card laid out so the connector is on the right hand side should have pins 1 and 2 as the top pair, 49 & 50 the bottom, and the connector on the component side.
Mechanical layout is not strictly bound by the bus layout and design, but to allow for card supports, the following suggestions apply. On an expansion card, the center pair of pins (and thus the center of the connector) should be located 50mm from the edge closest to the connector pins 1 & 2. The card should leave space for a support raiser going 2.5mm in from the edge closest to pins 1 & 2, extending 20mm along that edge.
![]() Position of connector |
For connectors used to connect a system board and expansion or bus-board, the suggested arrangement is to use straight connectors placed on-edge, female connector on the system board (main bus) side, and male on the expansion (exp bus) side. This allows the main-bus card and the exp-bus card to lie in the same plane, without requiring expensive right-angle 2x25 socket headers.
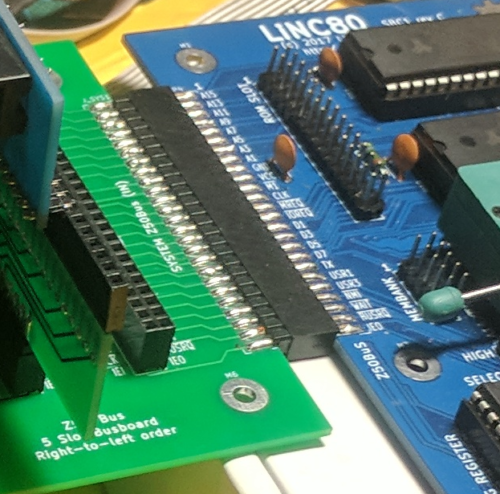
Example of on-edge connectors for joining a system board (right, female connector) to an expansion bus board (left, male connector)
Using the Z50Bus with the 6502
Being a bus for 8-bit microcomputers designed after 2016, the number of potential CPU's relevant for new designs is limited. Currently only the Z80-family and the 65x02 family of CPU's have parts still in production. Because of this, only a 65x02 adaption of the bus is suggested here.
Some of the Z80-style signals need to be synthesized. 65x02 uses memory mapped IO, so the IOReq signal needs to be generated by the CPU card/system when a request is made to the 65x02 IO address space selected for the system. The Mreq signal will then be a simple invert of the IOReq signal. An equivalent function of the WAIT and HALT signals may be found on the 65x02 RDY line. A diode split of the function may be appropriate. The SYNC signal can be adapted for the M1 signal function, if the INTAck feature is considered in the implementation.
65C02S signal | Z50Bus | Z80 signal | RC2014 |
*SYNC | M1 | M1 | N/A |
(generated) | MREQ | MREQ | MREQ |
(generated) | IOREQ | IOREQ | IOREQ |
*R/W | RD | RD | RD |
R/W | WR | WR | WR |
N/A | RFSH | RFSH | N/A |
(RDY) | HALT | HALT | N/A |
(RDY) | WAIT | WAIT | N/A |
INT | INT | INT | INT |
NMI | NMI | NMI | NMI |
RES | RST | RESET | RST |
BE (Jump) | BUSRQ | BUSRQ | N/A |
N/A | BUSAK | BUSAK | N/A |
PH2 (clk out) | CLK | CLK | CLK |
A0-A15* | A0-A15 | A0-A15 | A0-A15 |
D0-D7 | D0-D7 | D0-D7 | D0-D7 |
ML (Jump) | USR0 | ||
VP (Jump to GND) | |||
SO | USR1 |
There exists a 65c02 CPU card for the RC2014 system, this should be seen as the reference implementation when adapted to Z50Bus layout for the basic signals. See http://ancientcomputing.blogspot.no/2017/05/a-6502-cpu-for-rc2014-part-1.html. It is suggested that 65x02 based systems using the Z50Bus indicate clearly that not all expansion cards designed for a Z80 native Z50Bus system will be compatible.
56-pin STD Bus
For reference, I choose to include an image of the pinout/layout of the STD bus as it was used on the Ferguson Big Board II. The reason for including it, is that it was not easy to locate this information when I was researching, and I want to preserve this information. Note that the standardized STD interfaces use 80-pin card edge connectors, while the Big Board II used a 56 pin pin-header + header socket format with 2.54mm spacing
This is taken from the manual at http://www.bitsavers.org/pdf/ferguson/bigBoardII_Aug82.pdf. No further information is given in the manual.
Fake electronic components, a hazard of online shopping

This adventure started with a plan, and a bit of drafted design, to make a homebrew computer based on a Z80 CPU, and related components. But, I didn't actually have a Z80 chip yet! So, being cheap, I got the idea that going to eBay to find the needed components would be a great idea. Boy was I wrong.
After looking over my ideas, I searched eBay, and came up with a list of orders for central parts: A pair of Z80C0020 CPUs for $3.35, a Z84C4208 SIO/2 for $7.90, and five HM628128LP RAM chips for $6.0. All items from sellers providing free international shipping! The money left my account in december of '15.
As with all orders that include free international shipping, delivery time was a few weeks, so the project was put on a back-burner. When the parts arrived in early february, I was already well into other projects. So I gave them a quick look, everything seemed in order, and I packed them in my parts bin to wait. For nearly a full year.
When winter came around in 2016 and Christmas was approaching, it was time to start a winter-project. The Z80 homebrew project was resurrected, the components were dug out from the parts bin, and the first test-circuit was wired up on a set of breadboards purchased at bottom-price sometime during summer. A test-setup for this CPU is extremely simple. In the Z80/8080 instruction sets, the opcode 0x00, 0b00000000 is a NOP, so simply making all data-bus pins be tied to ground makes the CPU NOP its way through all 65536 addresses! So: behold the test-setup..
I checked, and checked again that I had the pinouts and connections right, made sure my bench power-supply was set to 4.99Volts, and examined my documentation to see that I should expect about 5-30mA current, LEDs not included. Next I connected my VCC from the power-supply to the setup, and immediately ripped the wired back off. The powersupply screamed 800mA at me! What could be causing my simple test circuit to draw 10-20 times as much current than I expected?
My first suspect was of course my wiring. So I checked that again. Pin-for-pin it was correct. The second suspect was the cheap breadboards, and the doublesided tape that stuck them to a wooden board. To eliminate those, I moved the circuit to a "known good" set of breadboards, part of an electronics trainer. After again checking the wiring, power was applied, and again the circuit pulled 6-800mA, and none of the LEDs lit up.
Next suspect was the Z80 chip itself. It could easily have been zapped by static during shipping, so I was happy I had ordered two, and slapped the second one on. This time, the power-supply reported a draw of 10mA, with a dim glow from one of the LEDs. Weird. I pondered for a moment, and just a moment long enough... Suddenly the current consumption rose to some high value I can't remember, and the famous, magical blue smoke appeared out of the Z80. Two for two...
As I now didn't have a CPU to use in the project, I decided to look up what the Z80 would cost from the reputable sources. After seeing that Mouser, DigiKey and RS Online all had the Z84C0010PEG in stock, I selected to order two from DigiKey for a total of $12, plus just about $18 for shipping. So, close to 10 times more than I paid for the two duds from eBay. But unlike the first two that took around 25 days to arrive and were non-functional, DigiKey had the parts in my mailbox some 50 hours after ordering, transported from the UK to Norway. And when I inserted one of them in the test circuit, it worked flawlessly, and pulled just under 28mA.
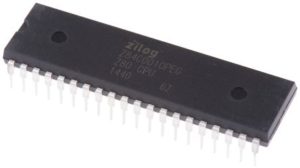
Z84C0010PEG, genuine
With a sneaking suspicion that less than $10 for the SIO/2 delivered might be a very optimistic price, I decided to test that one with only the supply voltage applied to the VCC/GND pins. I was most certainly correct. Just under an amp was being pulled, and the chip got very hot indeed (but did not release any magical smoke). Was I surprised? Well, the first time, with the CPU I was, even if the price had been very low indeed. But when the SIO/2 turned out to be a dud as well, I was not surprised.
The cheapskate in me had received a lesson: Always buy active semiconductor components from a proper, reputable source!
There's two types of semiconductor fakery going on: Clones of actual components, and outright fake duds. In the first group, you have things like the FTDI232/PL2303 fakes, where functional (but possibly crippled) semiconductor copies or clones are being manufactured and sold, as being the real deal. Some of these clones actually make their way into the mainstream supply chain of the official parts, sometimes because the original manufacturer "moonlights" poor-quality cheaper editions of the original.
The second type relies on online trade, cheapskates like me, or naive buyers. In this group, a seller looking to make a quick buck targets one or more reasonably popular but usually somewhat obscure components. They gets a hold of a bunch of very cheap components in the same package (like the DIP40 of a Z80). The cheap component will typically be a random IC that sells very cheaply, factory defects that can be picked from scrap heaps, or even old parts pulled from "recycling". With the package, they then clear away any markings on the package, and silk-print the markings of their "target". This convincing lookalike is then put up for sale, usually with a price placed around 1/2 of the "per one" price of sellers like DigiKey or Mouser.

Generic picture of Fake Z80
So, how does one spot the fake? Most of the time, simply looking at the price including shipping should be enough. If a component costs $6 plus shipping from Mouser, and sells for $2 including free international shipping, just walk away. It's going to be a fake. Also, if a seller is using the same stock, but not manufacturer, photo of the component as every other seller with the same device at the same price you're probably in muddy waters. Unfortunately it's not always that simple. Often times, the price is probable, and the photo looks convincing. And when you get the component in hand, the relabeling has been so well done you don't spot it. It really is a buyer beware situation.
With all these fake components going for cheap on eBay, does that mean that it is never OK to buy semiconductors there? I think it sometimes is OK. If the part has a realistic price, a plausible description, maybe even a unique photo taken by the seller, the probability of a good part goes up. As long as the seller is not located in China. Look for European or American sellers, Japan is typically also a "good source". In my experience, buying things from China is usually a decent experience EXCEPT for semiconductor parts. I've once received an IC, transistor or FET from China that was what I ordered...
Considering that a "realistic price" is typically the same as the price for a new component (or even higher) bought from DigiKey or Mouser, when would these "rules" for eBay-ing semiconductors apply? The answer to this is very simple: Non-active, obsolete parts. Sometimes you need an old part that's no longer in production. Trying to find a "good" seller of these is sometimes impossible, and if possible they are usually priced waaay expensive. So the best option for getting a decent price is going to eBay.
One example of mine of this is the AY-3-8910/YM2149. I have wanted to experiment with one of the "olde-time" 8-bit audio-chips, and looking over the various soundchip options I decided I wanted to try out the General Instruments AY-3-8910 or one of it's variants. Unfortunately the all of the AY-3-89xx chips, in GI or Microchip name, as well as the YM2149F have been out of production for several years. The only option of getting a hold of one is to get NOS or Pulled parts. I located a not-eBay seller (unfortunately I've lost the link) of genuine NOS AY-3-8912 chips. Unfortunately, paying $50 per chip was not something I felt like doing for a bit of experimentation. My limit was at $25. Going to eBay instead I located a chap in Germany that wanted $5 plus $1 shipping for one YM2149F. I also located a pair of sellers in China, one that wanted $8, free shipping for a Microchip AY-3-8910 and one that wanted $7 plus $2 shipping for an AY-3-8912. I ordered those three. When they arrived, I found out that the 8910 one was clearly a fake, while the 8912 and the 2149 both worked just fine!
There are a LOT of fake semiconductors on eBay and AliExpress. Generally, cheap, free-shipping components sold on these sites from mainland China are guaranteed to be fake. If the component you are looking for is still in active production, buy it from a proper electronics distributor like RS Components, DigiKey or Mouser. If the component you are looking for is obsolete/out of production, take care, research probable prices, and be critical to sellers location.
This post is part of a series documenting my journey in making my own homebrew computer, the posts can be found on this link.